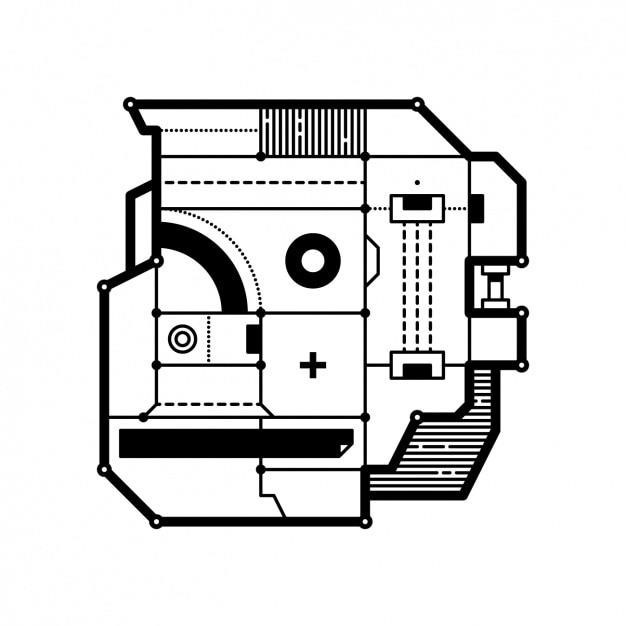
aircraft bulkhead structural integrity pdf
Aircraft Bulkhead Structural Integrity
An aircraft bulkhead is a structural component that divides the interior of an aircraft into compartments. It is typically made of metal or composite materials and plays a crucial role in maintaining the structural integrity of the aircraft. Bulkheads are essential for passenger and cargo safety, as they help to contain pressure differences and prevent catastrophic failure in the event of an accident. They also act as load-bearing elements, transferring forces from the fuselage to the wings and tail.
Importance of Bulkhead Integrity
The integrity of aircraft bulkheads is paramount to ensuring the safety and functionality of the aircraft. These structural elements are crucial for maintaining pressure differences within the cabin, especially during flight. They act as barriers to prevent catastrophic failure in the event of a decompression or other structural compromise. In the context of passenger and cargo safety, bulkheads play a vital role in containing potential damage and preventing the spread of fire or smoke.
Beyond their role in maintaining pressure and containing damage, bulkheads serve as load-bearing components, transferring forces from the fuselage to the wings and tail. They contribute to the overall structural strength and stability of the aircraft, ensuring its ability to withstand the stresses of flight. In the context of structural integrity programs, the inspection and maintenance of bulkheads are critical for identifying and addressing potential issues before they escalate into serious problems.
Maintaining the integrity of aircraft bulkheads is a crucial aspect of ensuring the safety and operational reliability of aircraft. Their role in maintaining pressure differences, containing damage, and contributing to overall structural strength makes them a critical component in the design and operation of aircraft.
Bulkhead Design Considerations
The design of aircraft bulkheads is a complex process that involves a multitude of factors, including structural strength, weight considerations, and ease of manufacturing. Designers must carefully consider the loads that the bulkhead will be subjected to during flight, including pressure differentials, impact loads, and fatigue stresses. The material selection is critical, with a balance between strength, weight, and cost being essential. Aluminum alloys, titanium, and composites are common materials used for bulkheads, each with their own advantages and disadvantages.
In addition to material selection, the geometry and configuration of the bulkhead are crucial design considerations. The shape, thickness, and reinforcement features are optimized to distribute loads effectively and prevent stress concentrations. The design must also accommodate access panels for maintenance and inspection, as well as provisions for mounting other components, such as seats, cargo systems, and emergency equipment. The design process often involves extensive analysis using finite element methods to predict the behavior of the bulkhead under various loading conditions.
The design of aircraft bulkheads is a meticulous process that involves careful consideration of numerous factors, ensuring the structural integrity, weight optimization, and functionality of this critical aircraft component.
Fatigue Testing and Limit of Validity
Fatigue testing is a crucial aspect of ensuring the structural integrity of aircraft bulkheads, especially considering the repetitive nature of flight cycles. These tests involve subjecting the bulkhead to cyclic loading that simulates the stresses experienced during normal flight operations. The goal is to determine the fatigue life of the bulkhead, which is the number of cycles it can withstand before failure. This information is critical for establishing the limit of validity (LOV), a key parameter in aircraft maintenance programs.
The LOV represents the operational limit based on fatigue test evidence that supports the maintenance program. It defines the period of time, typically measured in flight cycles or flight hours, up to which the aircraft’s structural integrity is guaranteed based on the fatigue testing data. The FAA, along with other aviation authorities, mandates that manufacturers establish LOVs for critical components like bulkheads, and provide inspection and repair procedures to prevent fatigue-related failures within the established LOV. Operators are then obligated to adhere to these maintenance programs to ensure the continued safety of their aircraft.
Fatigue testing and the determination of LOV are essential components of aircraft structural integrity programs, playing a vital role in ensuring the safety of passengers and crew by mitigating the risk of fatigue-related failures.
Aircraft Structural Integrity Programs
Aircraft structural integrity programs are comprehensive frameworks designed to ensure the continued airworthiness of aircraft throughout their service life. These programs address the critical aspects of maintaining the structural integrity of the aircraft, including the bulkheads, which are vital for passenger and cargo safety. They encompass a range of activities, from initial design and manufacturing to in-service inspections, maintenance, and repair.
A key component of these programs is the development of a structural integrity management plan, which outlines the strategies for monitoring and managing the structural health of the aircraft. This plan typically includes procedures for inspections, repairs, and modifications, as well as the establishment of limits of validity (LOVs) for critical components. LOVs are based on fatigue testing and provide a framework for determining when inspections or repairs are required to maintain structural integrity.
Aircraft structural integrity programs are essential for ensuring the safety and reliability of aircraft operations. They play a crucial role in preventing catastrophic failures, extending the service life of aircraft, and promoting the overall safety of air travel.
Case Studies and Accidents
The importance of bulkhead integrity is underscored by numerous case studies and accidents throughout aviation history. These incidents highlight the devastating consequences that can result from structural failures, particularly those involving the pressure bulkheads that maintain cabin pressure and integrity. One notable example is the Aloha Airlines Flight 243 incident in 1988, where a large section of the fuselage, including the forward pressure bulkhead, tore away during flight due to metal fatigue. This event, which resulted in a near-catastrophic failure and the loss of one passenger, led to significant advancements in aircraft inspection and maintenance procedures.
Another significant case is the British Airways Flight 9 incident in 1990, where a Boeing 747 experienced a rapid decompression after takeoff due to a failure in the rear pressure bulkhead. The cause of the failure was traced to a faulty repair that had been made to the bulkhead during a previous maintenance event. This incident, which resulted in the death of one passenger, reinforced the critical need for thorough inspections and repairs to ensure bulkhead integrity.
These and other similar accidents have underscored the importance of rigorous structural integrity programs and the need for robust design considerations to ensure the safe operation of aircraft.
Composite Bulkhead Design
The use of composite materials in aircraft design has revolutionized the industry, offering advantages in terms of weight reduction, strength-to-weight ratio, and corrosion resistance. Composite bulkheads, crafted from materials like carbon fiber reinforced plastic (CFRP), have gained increasing prominence in modern aircraft construction. These materials offer significant benefits over traditional metal bulkheads, including enhanced strength, lighter weight, and improved fatigue resistance. This translates into greater fuel efficiency and improved performance for aircraft.
The design and manufacturing of composite bulkheads require specialized expertise and advanced manufacturing techniques. The process often involves layering different types of composite materials, carefully controlling their orientation and arrangement to achieve the desired strength and stiffness characteristics. The use of advanced numerical analysis and simulation tools is crucial in optimizing the design of composite bulkheads, ensuring they meet stringent safety and performance standards.
The adoption of composite bulkheads has led to a paradigm shift in aircraft design, paving the way for lighter, more efficient, and safer aircraft.
Numerical Analysis and Simulation
Numerical analysis and simulation have become indispensable tools in modern aircraft design, particularly in evaluating the structural integrity of critical components like bulkheads. These techniques enable engineers to predict the behavior of a bulkhead under various loading conditions, including those encountered during flight, landing, and ground operations. This allows them to assess the bulkhead’s strength, stiffness, and potential for failure before any physical prototypes are built.
Finite element analysis (FEA) is a widely used numerical method for simulating the behavior of complex structures. In FEA, the bulkhead is divided into a mesh of small elements, each with its own material properties and loading conditions. The software then solves a set of equations to determine the stresses, strains, and displacements within each element. This provides a detailed picture of the bulkhead’s response to applied loads and helps identify potential areas of stress concentration or failure.
Numerical simulation allows engineers to optimize the design of bulkheads by exploring various configurations and material choices, leading to lighter, stronger, and more cost-effective designs. The use of these techniques has significantly enhanced the safety and reliability of aircraft, contributing to the overall success of the aerospace industry.
Maintenance and Inspection Procedures
Maintaining the structural integrity of an aircraft bulkhead is crucial for ensuring the safety of passengers and crew. Regular inspections and maintenance procedures play a vital role in identifying potential defects and preventing catastrophic failures. These procedures are guided by the aircraft manufacturer’s specifications and regulatory requirements. They are typically conducted at scheduled intervals, with the frequency and scope of inspections varying depending on factors such as the aircraft’s age, operating environment, and accumulated flight hours.
Visual inspections are a common practice, allowing for the detection of visible damage, corrosion, cracks, or other signs of deterioration. Non-destructive testing (NDT) methods, such as ultrasonic testing, eddy current testing, and radiographic inspection, can be employed to identify internal defects that are not readily visible. These methods use different physical principles to detect internal flaws or changes in material properties.
If defects are identified during inspection, they are typically repaired or replaced according to approved procedures; Repairs may involve patching, welding, or replacing damaged sections. The use of composite materials for repairs is becoming increasingly common, offering advantages in terms of weight reduction and corrosion resistance.
Impact of Corrosion on Structural Integrity
Corrosion is a significant threat to the structural integrity of aircraft bulkheads, particularly in environments with high humidity, salt spray, or exposure to de-icing fluids. Corrosion can weaken the material, reduce its load-bearing capacity, and create stress concentrations that can lead to fatigue cracks and eventual failure. The impact of corrosion on bulkhead integrity can be exacerbated by the presence of manufacturing defects, improper repairs, or inadequate maintenance practices.
Corrosion can occur in various forms, including pitting, galvanic corrosion, and crevice corrosion. Pitting corrosion is characterized by the formation of small holes or cavities on the surface of the material. Galvanic corrosion occurs when two dissimilar metals are in contact in the presence of an electrolyte, such as seawater. Crevice corrosion occurs in narrow gaps or crevices where moisture can become trapped and create a corrosive environment.
To mitigate the risk of corrosion, aircraft manufacturers employ various strategies, such as using corrosion-resistant materials, applying protective coatings, and implementing strict maintenance and inspection procedures. Regular inspections, including visual inspections and non-destructive testing, are essential for early detection of corrosion and timely repair. Corrosion control is crucial for ensuring the long-term safety and reliability of aircraft bulkheads.
Future Research and Development
Future research and development efforts in aircraft bulkhead structural integrity will focus on enhancing the performance and longevity of these critical components. One key area of focus is the development of advanced materials and manufacturing processes. This includes exploring new composites with improved strength-to-weight ratios, enhanced resistance to corrosion and fatigue, and greater damage tolerance. Advanced manufacturing techniques, such as additive manufacturing (3D printing), hold promise for creating complex geometries and optimized designs, potentially leading to lighter, stronger, and more durable bulkheads.
Another area of active research is the development of sophisticated numerical simulation and analysis tools. These tools will enable engineers to accurately predict the behavior of bulkheads under various loading conditions, including impact, fatigue, and corrosion. This will allow for more precise design optimization, reducing the need for expensive and time-consuming physical testing. Furthermore, the integration of advanced sensors and monitoring systems will facilitate real-time assessment of bulkhead health, enabling proactive maintenance and extending service life.
As the aviation industry strives for greater efficiency, sustainability, and safety, continued research and development efforts in aircraft bulkhead structural integrity are essential. The focus will be on achieving a balance between performance, weight, cost, and environmental impact, while ensuring the utmost safety for passengers and crew.
Comments (0)